Common Production Process of Pulse Capacitors
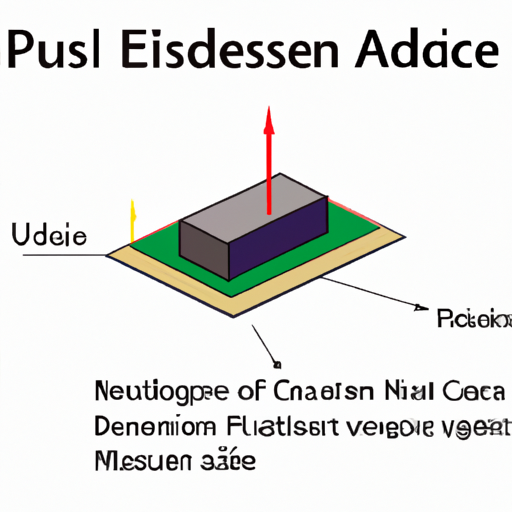
I. Introduction
Pulse capacitors are specialized components designed to handle high-voltage and high-current pulses, making them indispensable in a variety of applications, including power electronics, medical devices, and telecommunications. These capacitors are engineered to withstand rapid changes in voltage and current, ensuring reliable performance in demanding environments. Understanding the common production process of pulse capacitors is crucial for manufacturers and engineers alike, as it directly impacts the reliability and efficiency of these components. This blog post will delve into the various stages involved in the production of pulse capacitors, from raw material selection to final testing and distribution.
II. Raw Materials
The production of pulse capacitors begins with the careful selection of high-quality raw materials. The primary materials used in pulse capacitors include dielectric materials and conductive materials for the electrodes.
A. Types of Materials Used
1. **Dielectric Materials**: The dielectric material serves as an insulator, preventing electrical current from passing through while allowing the capacitor to store energy. Common dielectric materials used in pulse capacitors include:
- **Polyester**: Known for its good electrical properties and thermal stability.
- **Polypropylene**: Offers low dielectric losses and high insulation resistance.
- **Ceramic**: Provides excellent temperature stability and high dielectric strength.
2. **Conductive Materials**: The electrodes of pulse capacitors are typically made from conductive materials such as aluminum or copper. These materials are chosen for their excellent conductivity and ability to form a strong bond with the dielectric layers.
B. Quality Control of Raw Materials
Quality control is paramount during the raw material selection process. The performance of the final product heavily relies on the purity and consistency of these materials. Manufacturers often conduct rigorous testing to ensure that the raw materials meet specific standards and specifications. This includes checking for impurities, measuring dielectric strength, and assessing thermal properties.
C. Sourcing and Supply Chain Considerations
Sourcing high-quality raw materials is critical for maintaining production efficiency and product reliability. Manufacturers must establish strong relationships with suppliers to ensure a steady flow of materials. Additionally, supply chain logistics play a significant role in the timely delivery of materials, which can impact production schedules.
III. Design and Engineering
Before manufacturing begins, the design and engineering phase is critical. This phase involves defining the specifications and requirements of the pulse capacitors, such as voltage ratings and capacitance values.
A. Specifications and Requirements
1. **Voltage Ratings**: Pulse capacitors must be designed to handle specific voltage levels. Engineers must consider the maximum voltage the capacitor will encounter in its application to ensure safety and reliability.
2. **Capacitance Values**: The capacitance value determines how much energy the capacitor can store. Engineers must calculate the required capacitance based on the application’s needs.
B. Simulation and Modeling
Engineers often use simulation and modeling software to predict the performance of the capacitors under various conditions. This allows them to identify potential issues and optimize the design before moving to the manufacturing stage.
C. Prototyping and Testing
Prototyping is an essential step in the design process. Engineers create initial prototypes of the pulse capacitors to conduct testing and validation. This phase helps identify any design flaws and allows for adjustments before full-scale production begins.
IV. Manufacturing Process
The manufacturing process of pulse capacitors can be broken down into several key steps:
A. Dielectric Layer Production
The first step involves preparing the dielectric material. This may include processes like extrusion or film casting, depending on the type of dielectric used. The dielectric layer is then formed using techniques such as vacuum deposition or lamination, ensuring uniform thickness and properties.
B. Electrode Fabrication
The next step is the fabrication of the electrodes. Manufacturers select conductive materials, often metals like aluminum or copper, and employ deposition methods such as sputtering or chemical vapor deposition to create thin, uniform layers. This step is crucial for ensuring optimal electrical performance.
C. Assembly of Capacitor Components
Once the dielectric and electrodes are prepared, the assembly process begins. This involves stacking the dielectric layers and electrodes in a specific configuration. Connection techniques such as welding or soldering are employed to ensure electrical continuity and mechanical stability.
V. Encapsulation and Protection
After assembly, the capacitors undergo encapsulation to protect them from environmental factors and mechanical stress.
A. Purpose of Encapsulation
Encapsulation serves multiple purposes, including protecting the capacitor from moisture, dust, and physical damage. It also helps to enhance the dielectric properties and thermal stability of the capacitor.
B. Materials Used for Encapsulation
The encapsulation process typically involves applying a protective coating or housing made from materials like epoxy or silicone. These materials are chosen for their excellent insulating properties and durability.
C. Techniques for Encapsulation
Manufacturers may use various techniques for encapsulation, including potting, molding, or coating. The choice of technique depends on the specific requirements of the application and the environmental conditions the capacitor will face.
VI. Testing and Quality Assurance
Quality assurance is a vital part of the production process. Manufacturers conduct various tests to ensure the capacitors meet performance standards.
A. Electrical Testing
1. **Capacitance Measurement**: This test measures the actual capacitance of the capacitor to ensure it meets the specified values.
2. **Voltage Withstand Testing**: This test verifies that the capacitor can handle its rated voltage without failure.
B. Environmental Testing
Environmental testing assesses the capacitors' performance under extreme conditions. This includes:
1. **Temperature and Humidity Tests**: These tests evaluate how the capacitors perform in high-temperature and high-humidity environments.
2. **Mechanical Stress Tests**: These tests assess the capacitors' durability under mechanical stress, such as vibration or shock.
C. Compliance with Industry Standards
Compliance with industry standards, such as IEC or UL certifications, is essential to ensure safety and reliability. Manufacturers must adhere to these standards throughout the production process to guarantee that their products meet the necessary safety and performance criteria.
VII. Packaging and Distribution
Once the capacitors pass all tests, they are packaged for distribution.
A. Packaging Requirements
Packaging must protect the capacitors during transport and storage while providing necessary information for customers. Manufacturers often use anti-static materials and cushioning to prevent damage.
B. Logistics and Distribution Channels
Establishing efficient logistics and distribution channels is crucial for timely delivery to clients. Manufacturers must coordinate with shipping companies and distributors to ensure that products reach their destinations safely and on time.
C. Customer Support and Documentation
Providing customer support and documentation is essential for helping customers effectively use the capacitors in their applications. This includes datasheets, installation guidelines, and technical support to address any questions or concerns.
VIII. Conclusion
The production process of pulse capacitors is a complex and multi-faceted operation that requires careful attention to detail at every stage. From selecting high-quality raw materials to rigorous testing and quality assurance, each step plays a critical role in ensuring the reliability and performance of the final product. As technology advances, manufacturers must stay abreast of new materials and production techniques to enhance the efficiency and effectiveness of pulse capacitors. Continuous improvement in production processes will be essential to meet the evolving demands of various industries and applications.
In conclusion, understanding the common production process of pulse capacitors not only helps manufacturers optimize their operations but also ensures that engineers can select the right components for their applications, ultimately leading to more reliable and efficient systems.
Common Production Process of Pulse Capacitors
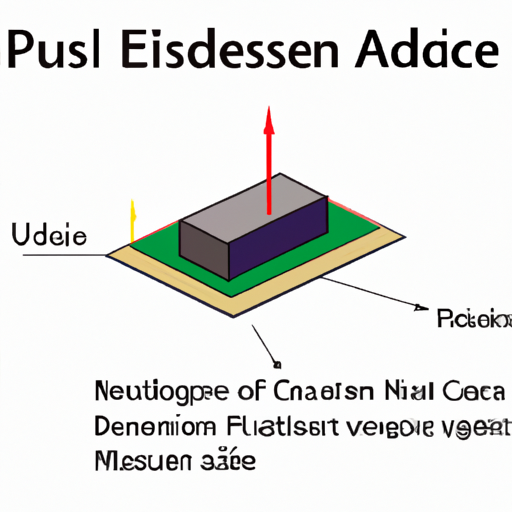
I. Introduction
Pulse capacitors are specialized components designed to handle high-voltage and high-current pulses, making them indispensable in a variety of applications, including power electronics, medical devices, and telecommunications. These capacitors are engineered to withstand rapid changes in voltage and current, ensuring reliable performance in demanding environments. Understanding the common production process of pulse capacitors is crucial for manufacturers and engineers alike, as it directly impacts the reliability and efficiency of these components. This blog post will delve into the various stages involved in the production of pulse capacitors, from raw material selection to final testing and distribution.
II. Raw Materials
The production of pulse capacitors begins with the careful selection of high-quality raw materials. The primary materials used in pulse capacitors include dielectric materials and conductive materials for the electrodes.
A. Types of Materials Used
1. **Dielectric Materials**: The dielectric material serves as an insulator, preventing electrical current from passing through while allowing the capacitor to store energy. Common dielectric materials used in pulse capacitors include:
- **Polyester**: Known for its good electrical properties and thermal stability.
- **Polypropylene**: Offers low dielectric losses and high insulation resistance.
- **Ceramic**: Provides excellent temperature stability and high dielectric strength.
2. **Conductive Materials**: The electrodes of pulse capacitors are typically made from conductive materials such as aluminum or copper. These materials are chosen for their excellent conductivity and ability to form a strong bond with the dielectric layers.
B. Quality Control of Raw Materials
Quality control is paramount during the raw material selection process. The performance of the final product heavily relies on the purity and consistency of these materials. Manufacturers often conduct rigorous testing to ensure that the raw materials meet specific standards and specifications. This includes checking for impurities, measuring dielectric strength, and assessing thermal properties.
C. Sourcing and Supply Chain Considerations
Sourcing high-quality raw materials is critical for maintaining production efficiency and product reliability. Manufacturers must establish strong relationships with suppliers to ensure a steady flow of materials. Additionally, supply chain logistics play a significant role in the timely delivery of materials, which can impact production schedules.
III. Design and Engineering
Before manufacturing begins, the design and engineering phase is critical. This phase involves defining the specifications and requirements of the pulse capacitors, such as voltage ratings and capacitance values.
A. Specifications and Requirements
1. **Voltage Ratings**: Pulse capacitors must be designed to handle specific voltage levels. Engineers must consider the maximum voltage the capacitor will encounter in its application to ensure safety and reliability.
2. **Capacitance Values**: The capacitance value determines how much energy the capacitor can store. Engineers must calculate the required capacitance based on the application’s needs.
B. Simulation and Modeling
Engineers often use simulation and modeling software to predict the performance of the capacitors under various conditions. This allows them to identify potential issues and optimize the design before moving to the manufacturing stage.
C. Prototyping and Testing
Prototyping is an essential step in the design process. Engineers create initial prototypes of the pulse capacitors to conduct testing and validation. This phase helps identify any design flaws and allows for adjustments before full-scale production begins.
IV. Manufacturing Process
The manufacturing process of pulse capacitors can be broken down into several key steps:
A. Dielectric Layer Production
The first step involves preparing the dielectric material. This may include processes like extrusion or film casting, depending on the type of dielectric used. The dielectric layer is then formed using techniques such as vacuum deposition or lamination, ensuring uniform thickness and properties.
B. Electrode Fabrication
The next step is the fabrication of the electrodes. Manufacturers select conductive materials, often metals like aluminum or copper, and employ deposition methods such as sputtering or chemical vapor deposition to create thin, uniform layers. This step is crucial for ensuring optimal electrical performance.
C. Assembly of Capacitor Components
Once the dielectric and electrodes are prepared, the assembly process begins. This involves stacking the dielectric layers and electrodes in a specific configuration. Connection techniques such as welding or soldering are employed to ensure electrical continuity and mechanical stability.
V. Encapsulation and Protection
After assembly, the capacitors undergo encapsulation to protect them from environmental factors and mechanical stress.
A. Purpose of Encapsulation
Encapsulation serves multiple purposes, including protecting the capacitor from moisture, dust, and physical damage. It also helps to enhance the dielectric properties and thermal stability of the capacitor.
B. Materials Used for Encapsulation
The encapsulation process typically involves applying a protective coating or housing made from materials like epoxy or silicone. These materials are chosen for their excellent insulating properties and durability.
C. Techniques for Encapsulation
Manufacturers may use various techniques for encapsulation, including potting, molding, or coating. The choice of technique depends on the specific requirements of the application and the environmental conditions the capacitor will face.
VI. Testing and Quality Assurance
Quality assurance is a vital part of the production process. Manufacturers conduct various tests to ensure the capacitors meet performance standards.
A. Electrical Testing
1. **Capacitance Measurement**: This test measures the actual capacitance of the capacitor to ensure it meets the specified values.
2. **Voltage Withstand Testing**: This test verifies that the capacitor can handle its rated voltage without failure.
B. Environmental Testing
Environmental testing assesses the capacitors' performance under extreme conditions. This includes:
1. **Temperature and Humidity Tests**: These tests evaluate how the capacitors perform in high-temperature and high-humidity environments.
2. **Mechanical Stress Tests**: These tests assess the capacitors' durability under mechanical stress, such as vibration or shock.
C. Compliance with Industry Standards
Compliance with industry standards, such as IEC or UL certifications, is essential to ensure safety and reliability. Manufacturers must adhere to these standards throughout the production process to guarantee that their products meet the necessary safety and performance criteria.
VII. Packaging and Distribution
Once the capacitors pass all tests, they are packaged for distribution.
A. Packaging Requirements
Packaging must protect the capacitors during transport and storage while providing necessary information for customers. Manufacturers often use anti-static materials and cushioning to prevent damage.
B. Logistics and Distribution Channels
Establishing efficient logistics and distribution channels is crucial for timely delivery to clients. Manufacturers must coordinate with shipping companies and distributors to ensure that products reach their destinations safely and on time.
C. Customer Support and Documentation
Providing customer support and documentation is essential for helping customers effectively use the capacitors in their applications. This includes datasheets, installation guidelines, and technical support to address any questions or concerns.
VIII. Conclusion
The production process of pulse capacitors is a complex and multi-faceted operation that requires careful attention to detail at every stage. From selecting high-quality raw materials to rigorous testing and quality assurance, each step plays a critical role in ensuring the reliability and performance of the final product. As technology advances, manufacturers must stay abreast of new materials and production techniques to enhance the efficiency and effectiveness of pulse capacitors. Continuous improvement in production processes will be essential to meet the evolving demands of various industries and applications.
In conclusion, understanding the common production process of pulse capacitors not only helps manufacturers optimize their operations but also ensures that engineers can select the right components for their applications, ultimately leading to more reliable and efficient systems.