What are the Latest Manufacturing Processes for Capacitors?
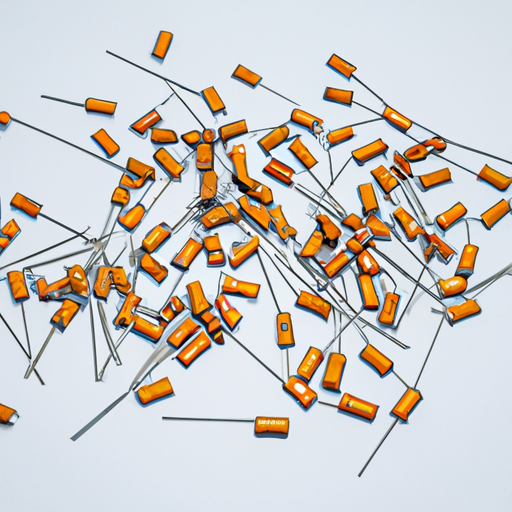
I. Introduction
Capacitors are essential components in electronic circuits, serving as energy storage devices that can release energy quickly when needed. They play a crucial role in various applications, from power supply smoothing to signal coupling and decoupling. As technology advances, the demand for capacitors with improved performance and reliability has led to significant innovations in manufacturing processes. This article explores the latest advancements in capacitor manufacturing, highlighting the evolution of materials, techniques, and technologies that are shaping the future of this vital industry.
II. Historical Context
The history of capacitor manufacturing dates back to the early 18th century with the invention of the Leyden jar, one of the first capacitors. Over the decades, capacitor technology has evolved significantly, transitioning from simple glass jars to complex multilayer ceramic capacitors and electrolytic capacitors. The materials used in capacitor production have also changed, moving from basic metals and ceramics to advanced polymers and nanomaterials. This evolution has been driven by the increasing demands of modern electronics, necessitating more efficient and reliable capacitors.
III. Types of Capacitors
Capacitors come in various types, each with unique characteristics and manufacturing processes. The most common types include:
Ceramic Capacitors: These are made from ceramic materials and are known for their stability and reliability. The manufacturing process involves layering ceramic and metal electrodes, followed by sintering at high temperatures.
Electrolytic Capacitors: These capacitors use an electrolyte to achieve high capacitance values. The manufacturing process includes anodizing aluminum or tantalum to create a dielectric layer.
Film Capacitors: Made from plastic films, these capacitors are known for their low losses and high voltage ratings. The manufacturing process involves winding or stacking layers of film and metal foil.
Tantalum Capacitors: These are similar to electrolytic capacitors but use tantalum as the anode material. The manufacturing process includes powder metallurgy techniques to create tantalum pellets.
Selecting the right manufacturing process is crucial for ensuring that the capacitor meets the specific requirements of its application, such as capacitance, voltage rating, and temperature stability.
IV. Advanced Materials in Capacitor Manufacturing
Recent advancements in materials science have led to the development of new dielectric and electrode materials that significantly enhance capacitor performance.
A. Development of New Dielectric Materials
1. **High-k Dielectrics**: High-k dielectrics, such as hafnium oxide, offer increased capacitance in smaller form factors. These materials allow for the miniaturization of capacitors without sacrificing performance.
2. **Nanomaterials**: The incorporation of nanomaterials, such as carbon nanotubes and graphene, has shown promise in improving capacitance and energy density. These materials can enhance the surface area and conductivity of electrodes, leading to better performance.
B. Innovations in Electrode Materials
1. **Conductive Polymers**: Conductive polymers are being explored as alternatives to traditional metal electrodes. They offer flexibility and can be processed at lower temperatures, making them suitable for various applications.
2. **Graphene and Carbon Nanotubes**: These materials are known for their exceptional electrical conductivity and mechanical strength. Their use in capacitor manufacturing can lead to lighter, more efficient devices.
The advancements in materials not only improve the performance of capacitors but also open up new possibilities for their applications in emerging technologies.
V. Modern Manufacturing Techniques
The manufacturing landscape for capacitors has been transformed by modern techniques that enhance efficiency and scalability.
A. Thin-Film Technology
Thin-film technology involves depositing thin layers of dielectric and electrode materials onto a substrate. This process allows for precise control over the thickness and composition of the layers, resulting in capacitors with improved performance characteristics. Thin-film capacitors are particularly advantageous in high-frequency applications due to their low equivalent series resistance (ESR).
B. Roll-to-Roll Manufacturing
Roll-to-roll (R2R) manufacturing is a continuous process that allows for the production of capacitors on flexible substrates. This technique is particularly beneficial for large-scale production, as it reduces material waste and increases throughput. R2R manufacturing is ideal for applications in flexible electronics and wearable devices.
C. 3D Printing in Capacitor Manufacturing
3D printing is an emerging technology in capacitor manufacturing, enabling the creation of complex geometries and customized designs. This technique allows for rapid prototyping and the production of capacitors tailored to specific applications. While still in its infancy, 3D printing holds great potential for revolutionizing capacitor design and manufacturing.
VI. Automation and Industry 4.0
The integration of automation and Industry 4.0 principles is reshaping capacitor manufacturing, enhancing efficiency and quality.
A. Role of Automation in Capacitor Manufacturing
Automation plays a crucial role in modern capacitor production, with robotics and artificial intelligence (AI) being employed to streamline processes. Automated production lines can operate with high precision, reducing the risk of human error and increasing output.
B. Integration of Industry 4.0 Principles
The concept of smart factories, driven by the Internet of Things (IoT), is becoming increasingly prevalent in capacitor manufacturing. IoT applications enable real-time monitoring of production processes, allowing for data analytics to optimize operations and improve quality control. This integration leads to more efficient manufacturing and reduced downtime.
VII. Environmental Considerations
As the electronics industry faces increasing scrutiny regarding its environmental impact, capacitor manufacturers are adopting sustainable practices.
A. Sustainable Manufacturing Practices
1. **Reduction of Waste and Energy Consumption**: Manufacturers are implementing lean manufacturing principles to minimize waste and energy usage. This includes optimizing production processes and recycling materials whenever possible.
2. **Use of Eco-Friendly Materials**: The development of biodegradable and recyclable materials for capacitors is gaining traction. These materials can help reduce the environmental footprint of capacitor production.
B. Regulatory Compliance and Environmental Impact Assessments
Manufacturers are also focusing on compliance with environmental regulations and conducting impact assessments to ensure their processes are sustainable. This proactive approach not only meets regulatory requirements but also enhances the company's reputation.
C. Future Trends in Sustainable Capacitor Manufacturing
The future of capacitor manufacturing will likely see a continued emphasis on sustainability, with innovations aimed at reducing environmental impact while maintaining performance and reliability.
VIII. Challenges and Future Directions
Despite the advancements in capacitor manufacturing, several challenges remain.
A. Current Challenges in Capacitor Manufacturing
1. **Cost Pressures and Material Shortages**: The rising costs of raw materials and supply chain disruptions pose significant challenges for manufacturers. Balancing cost-effectiveness with performance is a critical concern.
2. **Balancing Performance with Sustainability**: As manufacturers strive to adopt sustainable practices, they must also ensure that the performance of capacitors is not compromised. This balancing act requires ongoing research and innovation.
B. Future Trends and Innovations to Watch
1. **Potential Breakthroughs in Materials and Processes**: Ongoing research in materials science may lead to the discovery of new dielectrics and electrode materials that further enhance capacitor performance.
2. **The Role of Research and Development**: Investment in R&D will be crucial for driving innovation in capacitor manufacturing. Collaborations between academia and industry can accelerate the development of new technologies and processes.
IX. Conclusion
The advancements in manufacturing processes for capacitors are transforming the electronics industry, enabling the production of more efficient, reliable, and sustainable devices. As technology continues to evolve, the importance of these advancements cannot be overstated. The future of capacitor manufacturing holds great promise, with innovations in materials, techniques, and automation paving the way for new applications and improved performance. As we look ahead, it is clear that the capacitor manufacturing landscape will continue to evolve, shaping the future of technology in profound ways.
X. References
1. Smith, J. (2022). "Advancements in Capacitor Technology: A Review." *Journal of Electronic Materials*.
2. Johnson, L. (2023). "Sustainable Practices in Capacitor Manufacturing." *Environmental Science & Technology*.
3. Lee, A., & Chen, R. (2023). "The Role of Nanomaterials in Modern Capacitors." *Materials Today*.
4. Patel, S. (2023). "Industry 4.0 and Its Impact on Electronics Manufacturing." *IEEE Transactions on Industrial Electronics*.
What are the Latest Manufacturing Processes for Capacitors?
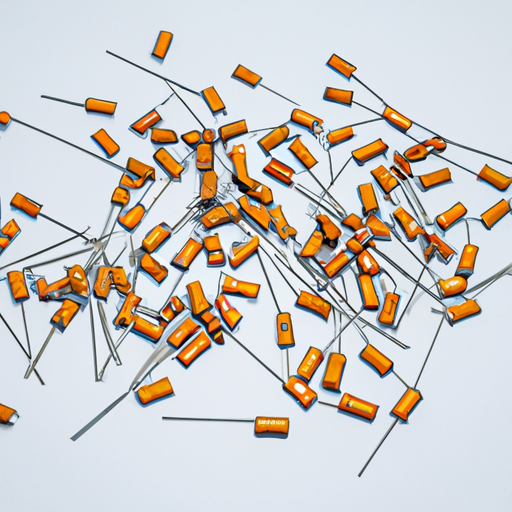
I. Introduction
Capacitors are essential components in electronic circuits, serving as energy storage devices that can release energy quickly when needed. They play a crucial role in various applications, from power supply smoothing to signal coupling and decoupling. As technology advances, the demand for capacitors with improved performance and reliability has led to significant innovations in manufacturing processes. This article explores the latest advancements in capacitor manufacturing, highlighting the evolution of materials, techniques, and technologies that are shaping the future of this vital industry.
II. Historical Context
The history of capacitor manufacturing dates back to the early 18th century with the invention of the Leyden jar, one of the first capacitors. Over the decades, capacitor technology has evolved significantly, transitioning from simple glass jars to complex multilayer ceramic capacitors and electrolytic capacitors. The materials used in capacitor production have also changed, moving from basic metals and ceramics to advanced polymers and nanomaterials. This evolution has been driven by the increasing demands of modern electronics, necessitating more efficient and reliable capacitors.
III. Types of Capacitors
Capacitors come in various types, each with unique characteristics and manufacturing processes. The most common types include:
Ceramic Capacitors: These are made from ceramic materials and are known for their stability and reliability. The manufacturing process involves layering ceramic and metal electrodes, followed by sintering at high temperatures.
Electrolytic Capacitors: These capacitors use an electrolyte to achieve high capacitance values. The manufacturing process includes anodizing aluminum or tantalum to create a dielectric layer.
Film Capacitors: Made from plastic films, these capacitors are known for their low losses and high voltage ratings. The manufacturing process involves winding or stacking layers of film and metal foil.
Tantalum Capacitors: These are similar to electrolytic capacitors but use tantalum as the anode material. The manufacturing process includes powder metallurgy techniques to create tantalum pellets.
Selecting the right manufacturing process is crucial for ensuring that the capacitor meets the specific requirements of its application, such as capacitance, voltage rating, and temperature stability.
IV. Advanced Materials in Capacitor Manufacturing
Recent advancements in materials science have led to the development of new dielectric and electrode materials that significantly enhance capacitor performance.
A. Development of New Dielectric Materials
1. **High-k Dielectrics**: High-k dielectrics, such as hafnium oxide, offer increased capacitance in smaller form factors. These materials allow for the miniaturization of capacitors without sacrificing performance.
2. **Nanomaterials**: The incorporation of nanomaterials, such as carbon nanotubes and graphene, has shown promise in improving capacitance and energy density. These materials can enhance the surface area and conductivity of electrodes, leading to better performance.
B. Innovations in Electrode Materials
1. **Conductive Polymers**: Conductive polymers are being explored as alternatives to traditional metal electrodes. They offer flexibility and can be processed at lower temperatures, making them suitable for various applications.
2. **Graphene and Carbon Nanotubes**: These materials are known for their exceptional electrical conductivity and mechanical strength. Their use in capacitor manufacturing can lead to lighter, more efficient devices.
The advancements in materials not only improve the performance of capacitors but also open up new possibilities for their applications in emerging technologies.
V. Modern Manufacturing Techniques
The manufacturing landscape for capacitors has been transformed by modern techniques that enhance efficiency and scalability.
A. Thin-Film Technology
Thin-film technology involves depositing thin layers of dielectric and electrode materials onto a substrate. This process allows for precise control over the thickness and composition of the layers, resulting in capacitors with improved performance characteristics. Thin-film capacitors are particularly advantageous in high-frequency applications due to their low equivalent series resistance (ESR).
B. Roll-to-Roll Manufacturing
Roll-to-roll (R2R) manufacturing is a continuous process that allows for the production of capacitors on flexible substrates. This technique is particularly beneficial for large-scale production, as it reduces material waste and increases throughput. R2R manufacturing is ideal for applications in flexible electronics and wearable devices.
C. 3D Printing in Capacitor Manufacturing
3D printing is an emerging technology in capacitor manufacturing, enabling the creation of complex geometries and customized designs. This technique allows for rapid prototyping and the production of capacitors tailored to specific applications. While still in its infancy, 3D printing holds great potential for revolutionizing capacitor design and manufacturing.
VI. Automation and Industry 4.0
The integration of automation and Industry 4.0 principles is reshaping capacitor manufacturing, enhancing efficiency and quality.
A. Role of Automation in Capacitor Manufacturing
Automation plays a crucial role in modern capacitor production, with robotics and artificial intelligence (AI) being employed to streamline processes. Automated production lines can operate with high precision, reducing the risk of human error and increasing output.
B. Integration of Industry 4.0 Principles
The concept of smart factories, driven by the Internet of Things (IoT), is becoming increasingly prevalent in capacitor manufacturing. IoT applications enable real-time monitoring of production processes, allowing for data analytics to optimize operations and improve quality control. This integration leads to more efficient manufacturing and reduced downtime.
VII. Environmental Considerations
As the electronics industry faces increasing scrutiny regarding its environmental impact, capacitor manufacturers are adopting sustainable practices.
A. Sustainable Manufacturing Practices
1. **Reduction of Waste and Energy Consumption**: Manufacturers are implementing lean manufacturing principles to minimize waste and energy usage. This includes optimizing production processes and recycling materials whenever possible.
2. **Use of Eco-Friendly Materials**: The development of biodegradable and recyclable materials for capacitors is gaining traction. These materials can help reduce the environmental footprint of capacitor production.
B. Regulatory Compliance and Environmental Impact Assessments
Manufacturers are also focusing on compliance with environmental regulations and conducting impact assessments to ensure their processes are sustainable. This proactive approach not only meets regulatory requirements but also enhances the company's reputation.
C. Future Trends in Sustainable Capacitor Manufacturing
The future of capacitor manufacturing will likely see a continued emphasis on sustainability, with innovations aimed at reducing environmental impact while maintaining performance and reliability.
VIII. Challenges and Future Directions
Despite the advancements in capacitor manufacturing, several challenges remain.
A. Current Challenges in Capacitor Manufacturing
1. **Cost Pressures and Material Shortages**: The rising costs of raw materials and supply chain disruptions pose significant challenges for manufacturers. Balancing cost-effectiveness with performance is a critical concern.
2. **Balancing Performance with Sustainability**: As manufacturers strive to adopt sustainable practices, they must also ensure that the performance of capacitors is not compromised. This balancing act requires ongoing research and innovation.
B. Future Trends and Innovations to Watch
1. **Potential Breakthroughs in Materials and Processes**: Ongoing research in materials science may lead to the discovery of new dielectrics and electrode materials that further enhance capacitor performance.
2. **The Role of Research and Development**: Investment in R&D will be crucial for driving innovation in capacitor manufacturing. Collaborations between academia and industry can accelerate the development of new technologies and processes.
IX. Conclusion
The advancements in manufacturing processes for capacitors are transforming the electronics industry, enabling the production of more efficient, reliable, and sustainable devices. As technology continues to evolve, the importance of these advancements cannot be overstated. The future of capacitor manufacturing holds great promise, with innovations in materials, techniques, and automation paving the way for new applications and improved performance. As we look ahead, it is clear that the capacitor manufacturing landscape will continue to evolve, shaping the future of technology in profound ways.
X. References
1. Smith, J. (2022). "Advancements in Capacitor Technology: A Review." *Journal of Electronic Materials*.
2. Johnson, L. (2023). "Sustainable Practices in Capacitor Manufacturing." *Environmental Science & Technology*.
3. Lee, A., & Chen, R. (2023). "The Role of Nanomaterials in Modern Capacitors." *Materials Today*.
4. Patel, S. (2023). "Industry 4.0 and Its Impact on Electronics Manufacturing." *IEEE Transactions on Industrial Electronics*.