The Production Process of Mainstream Capacitor Manufacturers
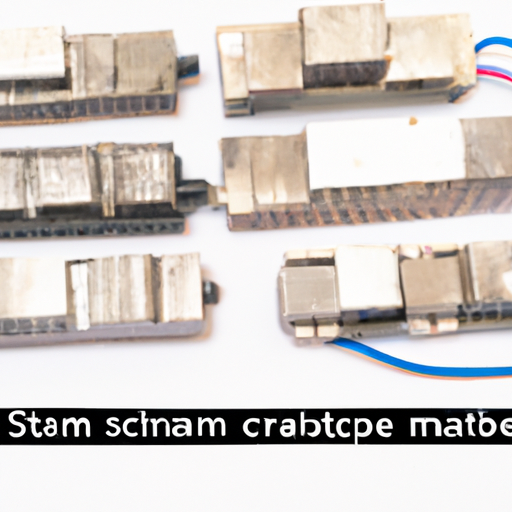
I. Introduction
Capacitors are fundamental components in electronic circuits, serving as energy storage devices that can release energy when needed. They play a crucial role in various applications, from smoothing out voltage fluctuations in power supplies to enabling signal coupling in audio equipment. The capacitor manufacturing industry has evolved significantly over the years, driven by advancements in technology and increasing demand for electronic devices. This article aims to explore the production process of mainstream capacitor manufacturers, shedding light on the intricate steps involved in creating these essential components.
II. Types of Capacitors
Capacitors come in various types, each designed for specific applications and performance characteristics. The most common types include:
Ceramic Capacitors: Known for their small size and high capacitance, ceramic capacitors are widely used in high-frequency applications.
Electrolytic Capacitors: These capacitors are polarized and offer high capacitance values, making them ideal for power supply applications.
Film Capacitors: Made from thin plastic films, these capacitors are known for their stability and low loss, often used in audio and RF applications.
Tantalum Capacitors: These capacitors are compact and reliable, commonly used in portable electronics due to their high capacitance-to-volume ratio.
Understanding the different types of capacitors is essential, as each type has a unique manufacturing process tailored to its specific materials and performance requirements.
III. Raw Materials
The production of capacitors begins with the selection of raw materials, which significantly influence the performance and reliability of the final product. The primary materials used in capacitor production include:
A. Dielectric Materials
Ceramics: Used in ceramic capacitors, these materials provide excellent dielectric properties and stability.
Polymers: Commonly used in film capacitors, polymers offer flexibility and a wide range of dielectric constants.
Electrolytes: Essential for electrolytic capacitors, electrolytes facilitate the flow of electric charge.
B. Conductive Materials
Metals: Aluminum and tantalum are commonly used as conductive materials in electrolytic and tantalum capacitors, respectively. Copper is often used in various capacitor types for its excellent conductivity.
C. Sourcing and Quality Control
Sourcing high-quality raw materials is critical for capacitor manufacturers. They often establish relationships with trusted suppliers and implement rigorous quality control measures to ensure that the materials meet industry standards. This step is vital, as the quality of raw materials directly impacts the performance and longevity of the capacitors produced.
IV. Design and Engineering
The design phase is crucial in determining the performance characteristics of capacitors. Engineers consider various factors, including size, capacitance, and voltage rating, to create designs that meet specific application requirements.
A. Role of Design in Capacitor Performance
The design of a capacitor influences its electrical characteristics, such as capacitance value, equivalent series resistance (ESR), and temperature stability. Engineers use computer-aided design (CAD) software to simulate and optimize designs before moving to prototyping.
B. Engineering Considerations
During the engineering phase, considerations such as the physical dimensions of the capacitor, the materials used, and the intended application are taken into account. This ensures that the final product meets the necessary specifications and performance standards.
C. Prototyping and Testing
Once a design is finalized, manufacturers create prototypes to test their performance. This phase involves rigorous testing to evaluate parameters such as capacitance, ESR, and leakage current. Any necessary adjustments are made before moving to full-scale production.
V. Manufacturing Process
The manufacturing process of capacitors involves several key steps, which can vary depending on the type of capacitor being produced. Below is an overview of the general manufacturing steps, followed by specific processes for different capacitor types.
A. General Manufacturing Steps
1. **Material Preparation**: Raw materials are prepared and processed to meet the specifications required for capacitor production.
2. **Layering and Assembly**: The prepared materials are layered and assembled to form the capacitor structure.
3. **Encapsulation and Packaging**: The assembled capacitors are encapsulated to protect them from environmental factors and then packaged for distribution.
B. Specific Processes for Different Types of Capacitors
1. Ceramic Capacitors
Powder Preparation and Pressing: Ceramic powders are mixed with additives and pressed into desired shapes.
Sintering and Electrode Application: The pressed shapes are sintered at high temperatures to achieve the desired dielectric properties, followed by the application of electrodes.
2. Electrolytic Capacitors
Anodization and Electrolyte Filling: Aluminum foils are anodized to form a dielectric layer, and electrolytes are filled into the capacitor casing.
Sealing and Testing: The capacitors are sealed to prevent leakage and undergo testing to ensure they meet performance standards.
3. Film Capacitors
Film Production and Metallization: Thin plastic films are produced and metallized to create electrodes.
Winding and Cutting: The metallized films are wound into cylindrical shapes and cut to the desired size.
4. Tantalum Capacitors
Tantalum Powder Preparation: Tantalum powder is prepared and compacted into desired shapes.
Sintering and Electrolyte Application: The compacted tantalum is sintered, and electrolytes are applied to create the final capacitor structure.
VI. Quality Control and Testing
Quality control is paramount in capacitor manufacturing, as even minor defects can lead to failures in electronic circuits. Manufacturers implement comprehensive quality assurance programs that include:
A. Importance of Quality Assurance
Quality assurance ensures that capacitors meet the required specifications and performance standards, reducing the risk of failures in end applications.
B. Common Testing Methods
Manufacturers employ various testing methods to evaluate capacitor performance, including:
Capacitance Testing: Measures the capacitor's ability to store charge.
Equivalent Series Resistance (ESR) Testing: Evaluates the internal resistance of the capacitor.
Leakage Current Testing: Assesses the amount of current that leaks through the dielectric material.
C. Compliance with Industry Standards
Capacitor manufacturers must comply with industry standards such as ISO and IEC to ensure their products are safe and reliable. Compliance involves regular audits and adherence to established testing protocols.
VII. Environmental Considerations
As the electronics industry grows, so does the need for sustainable manufacturing practices. Capacitor manufacturers are increasingly focusing on environmental considerations, including:
A. Sustainability in Capacitor Manufacturing
Manufacturers are adopting sustainable practices, such as reducing energy consumption and minimizing waste during production.
B. Waste Management and Recycling Practices
Effective waste management strategies are implemented to recycle materials and reduce the environmental impact of manufacturing processes.
C. Regulatory Compliance and Environmental Impact Assessments
Manufacturers must comply with environmental regulations and conduct impact assessments to ensure their operations do not harm the environment.
VIII. Conclusion
The production process of mainstream capacitor manufacturers is a complex and multifaceted endeavor that involves careful consideration of materials, design, engineering, and quality control. As technology continues to advance, manufacturers are constantly seeking ways to improve their processes and produce more efficient and reliable capacitors. The significance of these advancements cannot be overstated, as they have far-reaching implications for the electronics industry and the devices we rely on daily. Looking ahead, trends such as miniaturization, increased capacitance, and sustainability will shape the future of capacitor manufacturing, ensuring that these essential components continue to meet the demands of an ever-evolving technological landscape.
IX. References
For further exploration of capacitor manufacturing processes, consider the following resources:
1. "Capacitor Technology and Applications" - A comprehensive guide to capacitor types and their uses.
2. "Manufacturing Processes for Electronics" - An overview of manufacturing techniques in the electronics industry.
3. "Sustainable Practices in Electronics Manufacturing" - A resource on environmental considerations in the electronics sector.
This blog post provides a detailed overview of the production process of mainstream capacitor manufacturers, highlighting the importance of each step in creating reliable and efficient capacitors for various applications.
The Production Process of Mainstream Capacitor Manufacturers
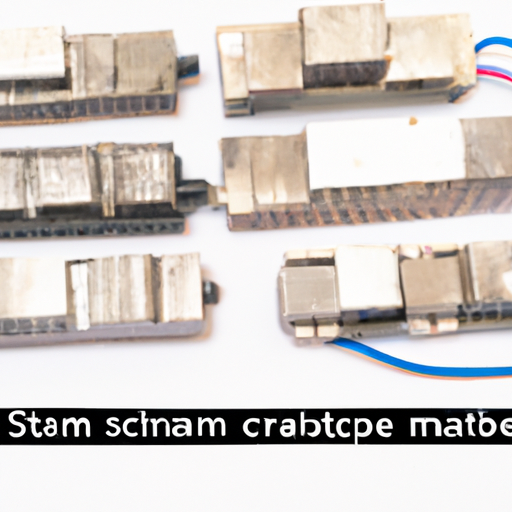
I. Introduction
Capacitors are fundamental components in electronic circuits, serving as energy storage devices that can release energy when needed. They play a crucial role in various applications, from smoothing out voltage fluctuations in power supplies to enabling signal coupling in audio equipment. The capacitor manufacturing industry has evolved significantly over the years, driven by advancements in technology and increasing demand for electronic devices. This article aims to explore the production process of mainstream capacitor manufacturers, shedding light on the intricate steps involved in creating these essential components.
II. Types of Capacitors
Capacitors come in various types, each designed for specific applications and performance characteristics. The most common types include:
Ceramic Capacitors: Known for their small size and high capacitance, ceramic capacitors are widely used in high-frequency applications.
Electrolytic Capacitors: These capacitors are polarized and offer high capacitance values, making them ideal for power supply applications.
Film Capacitors: Made from thin plastic films, these capacitors are known for their stability and low loss, often used in audio and RF applications.
Tantalum Capacitors: These capacitors are compact and reliable, commonly used in portable electronics due to their high capacitance-to-volume ratio.
Understanding the different types of capacitors is essential, as each type has a unique manufacturing process tailored to its specific materials and performance requirements.
III. Raw Materials
The production of capacitors begins with the selection of raw materials, which significantly influence the performance and reliability of the final product. The primary materials used in capacitor production include:
A. Dielectric Materials
Ceramics: Used in ceramic capacitors, these materials provide excellent dielectric properties and stability.
Polymers: Commonly used in film capacitors, polymers offer flexibility and a wide range of dielectric constants.
Electrolytes: Essential for electrolytic capacitors, electrolytes facilitate the flow of electric charge.
B. Conductive Materials
Metals: Aluminum and tantalum are commonly used as conductive materials in electrolytic and tantalum capacitors, respectively. Copper is often used in various capacitor types for its excellent conductivity.
C. Sourcing and Quality Control
Sourcing high-quality raw materials is critical for capacitor manufacturers. They often establish relationships with trusted suppliers and implement rigorous quality control measures to ensure that the materials meet industry standards. This step is vital, as the quality of raw materials directly impacts the performance and longevity of the capacitors produced.
IV. Design and Engineering
The design phase is crucial in determining the performance characteristics of capacitors. Engineers consider various factors, including size, capacitance, and voltage rating, to create designs that meet specific application requirements.
A. Role of Design in Capacitor Performance
The design of a capacitor influences its electrical characteristics, such as capacitance value, equivalent series resistance (ESR), and temperature stability. Engineers use computer-aided design (CAD) software to simulate and optimize designs before moving to prototyping.
B. Engineering Considerations
During the engineering phase, considerations such as the physical dimensions of the capacitor, the materials used, and the intended application are taken into account. This ensures that the final product meets the necessary specifications and performance standards.
C. Prototyping and Testing
Once a design is finalized, manufacturers create prototypes to test their performance. This phase involves rigorous testing to evaluate parameters such as capacitance, ESR, and leakage current. Any necessary adjustments are made before moving to full-scale production.
V. Manufacturing Process
The manufacturing process of capacitors involves several key steps, which can vary depending on the type of capacitor being produced. Below is an overview of the general manufacturing steps, followed by specific processes for different capacitor types.
A. General Manufacturing Steps
1. **Material Preparation**: Raw materials are prepared and processed to meet the specifications required for capacitor production.
2. **Layering and Assembly**: The prepared materials are layered and assembled to form the capacitor structure.
3. **Encapsulation and Packaging**: The assembled capacitors are encapsulated to protect them from environmental factors and then packaged for distribution.
B. Specific Processes for Different Types of Capacitors
1. Ceramic Capacitors
Powder Preparation and Pressing: Ceramic powders are mixed with additives and pressed into desired shapes.
Sintering and Electrode Application: The pressed shapes are sintered at high temperatures to achieve the desired dielectric properties, followed by the application of electrodes.
2. Electrolytic Capacitors
Anodization and Electrolyte Filling: Aluminum foils are anodized to form a dielectric layer, and electrolytes are filled into the capacitor casing.
Sealing and Testing: The capacitors are sealed to prevent leakage and undergo testing to ensure they meet performance standards.
3. Film Capacitors
Film Production and Metallization: Thin plastic films are produced and metallized to create electrodes.
Winding and Cutting: The metallized films are wound into cylindrical shapes and cut to the desired size.
4. Tantalum Capacitors
Tantalum Powder Preparation: Tantalum powder is prepared and compacted into desired shapes.
Sintering and Electrolyte Application: The compacted tantalum is sintered, and electrolytes are applied to create the final capacitor structure.
VI. Quality Control and Testing
Quality control is paramount in capacitor manufacturing, as even minor defects can lead to failures in electronic circuits. Manufacturers implement comprehensive quality assurance programs that include:
A. Importance of Quality Assurance
Quality assurance ensures that capacitors meet the required specifications and performance standards, reducing the risk of failures in end applications.
B. Common Testing Methods
Manufacturers employ various testing methods to evaluate capacitor performance, including:
Capacitance Testing: Measures the capacitor's ability to store charge.
Equivalent Series Resistance (ESR) Testing: Evaluates the internal resistance of the capacitor.
Leakage Current Testing: Assesses the amount of current that leaks through the dielectric material.
C. Compliance with Industry Standards
Capacitor manufacturers must comply with industry standards such as ISO and IEC to ensure their products are safe and reliable. Compliance involves regular audits and adherence to established testing protocols.
VII. Environmental Considerations
As the electronics industry grows, so does the need for sustainable manufacturing practices. Capacitor manufacturers are increasingly focusing on environmental considerations, including:
A. Sustainability in Capacitor Manufacturing
Manufacturers are adopting sustainable practices, such as reducing energy consumption and minimizing waste during production.
B. Waste Management and Recycling Practices
Effective waste management strategies are implemented to recycle materials and reduce the environmental impact of manufacturing processes.
C. Regulatory Compliance and Environmental Impact Assessments
Manufacturers must comply with environmental regulations and conduct impact assessments to ensure their operations do not harm the environment.
VIII. Conclusion
The production process of mainstream capacitor manufacturers is a complex and multifaceted endeavor that involves careful consideration of materials, design, engineering, and quality control. As technology continues to advance, manufacturers are constantly seeking ways to improve their processes and produce more efficient and reliable capacitors. The significance of these advancements cannot be overstated, as they have far-reaching implications for the electronics industry and the devices we rely on daily. Looking ahead, trends such as miniaturization, increased capacitance, and sustainability will shape the future of capacitor manufacturing, ensuring that these essential components continue to meet the demands of an ever-evolving technological landscape.
IX. References
For further exploration of capacitor manufacturing processes, consider the following resources:
1. "Capacitor Technology and Applications" - A comprehensive guide to capacitor types and their uses.
2. "Manufacturing Processes for Electronics" - An overview of manufacturing techniques in the electronics industry.
3. "Sustainable Practices in Electronics Manufacturing" - A resource on environmental considerations in the electronics sector.
This blog post provides a detailed overview of the production process of mainstream capacitor manufacturers, highlighting the importance of each step in creating reliable and efficient capacitors for various applications.