Common Production Processes for Resistor Standards
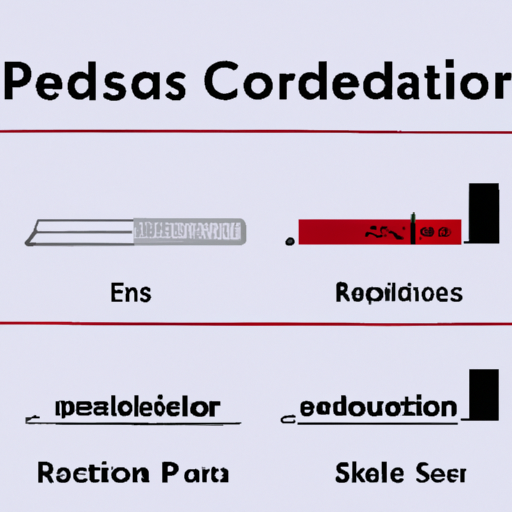
I. Introduction
Resistor standards are essential components in the world of electronics, serving as benchmarks for resistance values and ensuring the accuracy and reliability of electronic circuits. These standards are crucial for various applications, from consumer electronics to industrial machinery, where precise resistance values are necessary for optimal performance. The production of resistor standards involves a series of intricate processes that transform raw materials into high-precision components. This blog post will explore the common production processes for resistor standards, delving into the types of resistors, raw materials, fabrication techniques, quality control measures, and future trends in the industry.
II. Types of Resistor Standards
A. Wirewound Resistors
Wirewound resistors are made by winding a metal wire around a core, typically made of ceramic or fiberglass. These resistors are known for their high precision and stability, making them suitable for applications requiring accurate resistance values, such as in measurement instruments and power supplies.
B. Thin Film Resistors
Thin film resistors are created by depositing a thin layer of resistive material onto a substrate. This type of resistor offers excellent temperature stability and low noise, making it ideal for high-frequency applications and precision circuits.
C. Thick Film Resistors
Thick film resistors are produced by screen printing a paste of conductive material onto a substrate and then firing it to create a solid layer. These resistors are widely used in consumer electronics due to their cost-effectiveness and versatility.
D. Other Types
In addition to wirewound, thin film, and thick film resistors, there are other types, such as metal film and carbon film resistors. Each type has unique characteristics and applications, catering to different needs in the electronics industry.
III. Raw Materials Used in Resistor Production
A. Conductive Materials
The choice of conductive materials is critical in resistor production. Common metals used include nickel, copper, and tantalum, which provide the necessary conductivity and stability. Carbon-based materials are also popular, especially in carbon film resistors, due to their cost-effectiveness and good thermal stability.
B. Insulating Materials
Insulating materials play a vital role in ensuring the performance and reliability of resistors. Ceramics are commonly used for their excellent thermal and electrical insulating properties. Epoxy resins are also utilized, particularly in thick film resistors, to provide a protective layer.
C. Substrates
The substrate is the base material on which resistors are fabricated. Different types of substrates are used depending on the resistor type. For instance, ceramic substrates are often used for wirewound and thin film resistors, while glass and polymer substrates may be used for thick film resistors.
IV. Common Production Processes
A. Design and Prototyping
The production of resistor standards begins with design and prototyping. Engineers use Computer-Aided Design (CAD) tools to create detailed designs of the resistors. Simulation and testing of these designs are conducted to ensure they meet the required specifications before moving to the material preparation stage.
B. Material Preparation
Once the designs are finalized, the next step is material preparation. This involves sourcing and processing raw materials, ensuring they meet quality control measures. The quality of the materials directly impacts the performance and reliability of the final product.
C. Fabrication Techniques
The fabrication of resistors varies depending on the type being produced:
1. Wirewound Resistor Production
The production of wirewound resistors involves a winding process where a metal wire is carefully wound around a core. The resistance value is adjusted by changing the length and thickness of the wire. After winding, the resistor is often coated with an insulating material to protect it from environmental factors.
2. Thin Film Resistor Production
Thin film resistors are produced using deposition techniques such as sputtering or evaporation. A thin layer of resistive material is deposited onto the substrate, followed by patterning and etching to create the desired resistance value. This process allows for high precision and control over the resistor's characteristics.
3. Thick Film Resistor Production
Thick film resistors are made using a screen printing process, where a paste of conductive material is printed onto a substrate. The printed resistors are then fired in a kiln to cure the paste, creating a solid layer. This method is cost-effective and allows for mass production.
D. Assembly and Packaging
After fabrication, resistors are assembled and packaged. This involves mounting the resistors onto substrates, which may include circuit boards. Encapsulation and protective coatings are applied to enhance durability and protect against environmental factors.
E. Testing and Calibration
Testing and calibration are critical steps in the production process. Electrical testing methods are employed to verify the resistance values and ensure they meet specifications. Calibration against established standards is conducted to guarantee accuracy. Environmental testing is also performed to assess the resistors' performance under various conditions.
V. Quality Control and Standards Compliance
A. Importance of Quality Control in Resistor Production
Quality control is paramount in resistor production, as it ensures that the final products meet the required specifications and standards. Rigorous testing and inspection processes are implemented at various stages of production to identify and rectify any issues.
B. Industry Standards
Compliance with industry standards, such as ISO and IEC, is essential for resistor manufacturers. These standards provide guidelines for quality management, safety, and performance, ensuring that resistors are reliable and suitable for their intended applications.
C. Testing for Reliability and Longevity
Reliability testing is conducted to assess the long-term performance of resistors. This includes stress testing under extreme conditions to evaluate their durability and longevity. Manufacturers aim to produce resistors that can withstand the rigors of their operating environments.
VI. Innovations and Future Trends in Resistor Production
A. Advances in Materials Science
The field of materials science is continually evolving, leading to the development of new materials with enhanced properties. Innovations in conductive and insulating materials are expected to improve the performance and reliability of resistors.
B. Automation and Smart Manufacturing
Automation is becoming increasingly prevalent in resistor production, streamlining processes and reducing human error. Smart manufacturing technologies, such as IoT and AI, are being integrated into production lines to enhance efficiency and quality control.
C. Environmental Considerations and Sustainability
As the electronics industry faces growing environmental concerns, manufacturers are exploring sustainable practices in resistor production. This includes using eco-friendly materials, reducing waste, and implementing energy-efficient processes.
VII. Conclusion
In summary, the production of resistor standards involves a complex interplay of design, material selection, fabrication techniques, and quality control measures. Understanding these processes is crucial for appreciating the role of resistors in modern electronics. As technology continues to advance, the future of resistor production looks promising, with innovations in materials science, automation, and sustainability paving the way for more efficient and reliable components. Resistor standards will remain a cornerstone of electronic design, ensuring that devices operate accurately and effectively in an ever-evolving technological landscape.
VIII. References
- Academic Journals
- Industry Reports
- Standards Organizations Publications
This blog post provides a comprehensive overview of the common production processes for resistor standards, highlighting the importance of these components in the electronics industry and the intricate processes involved in their production.
Common Production Processes for Resistor Standards
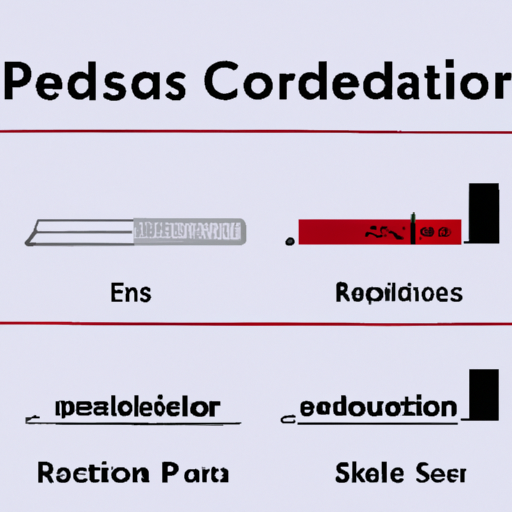
I. Introduction
Resistor standards are essential components in the world of electronics, serving as benchmarks for resistance values and ensuring the accuracy and reliability of electronic circuits. These standards are crucial for various applications, from consumer electronics to industrial machinery, where precise resistance values are necessary for optimal performance. The production of resistor standards involves a series of intricate processes that transform raw materials into high-precision components. This blog post will explore the common production processes for resistor standards, delving into the types of resistors, raw materials, fabrication techniques, quality control measures, and future trends in the industry.
II. Types of Resistor Standards
A. Wirewound Resistors
Wirewound resistors are made by winding a metal wire around a core, typically made of ceramic or fiberglass. These resistors are known for their high precision and stability, making them suitable for applications requiring accurate resistance values, such as in measurement instruments and power supplies.
B. Thin Film Resistors
Thin film resistors are created by depositing a thin layer of resistive material onto a substrate. This type of resistor offers excellent temperature stability and low noise, making it ideal for high-frequency applications and precision circuits.
C. Thick Film Resistors
Thick film resistors are produced by screen printing a paste of conductive material onto a substrate and then firing it to create a solid layer. These resistors are widely used in consumer electronics due to their cost-effectiveness and versatility.
D. Other Types
In addition to wirewound, thin film, and thick film resistors, there are other types, such as metal film and carbon film resistors. Each type has unique characteristics and applications, catering to different needs in the electronics industry.
III. Raw Materials Used in Resistor Production
A. Conductive Materials
The choice of conductive materials is critical in resistor production. Common metals used include nickel, copper, and tantalum, which provide the necessary conductivity and stability. Carbon-based materials are also popular, especially in carbon film resistors, due to their cost-effectiveness and good thermal stability.
B. Insulating Materials
Insulating materials play a vital role in ensuring the performance and reliability of resistors. Ceramics are commonly used for their excellent thermal and electrical insulating properties. Epoxy resins are also utilized, particularly in thick film resistors, to provide a protective layer.
C. Substrates
The substrate is the base material on which resistors are fabricated. Different types of substrates are used depending on the resistor type. For instance, ceramic substrates are often used for wirewound and thin film resistors, while glass and polymer substrates may be used for thick film resistors.
IV. Common Production Processes
A. Design and Prototyping
The production of resistor standards begins with design and prototyping. Engineers use Computer-Aided Design (CAD) tools to create detailed designs of the resistors. Simulation and testing of these designs are conducted to ensure they meet the required specifications before moving to the material preparation stage.
B. Material Preparation
Once the designs are finalized, the next step is material preparation. This involves sourcing and processing raw materials, ensuring they meet quality control measures. The quality of the materials directly impacts the performance and reliability of the final product.
C. Fabrication Techniques
The fabrication of resistors varies depending on the type being produced:
1. Wirewound Resistor Production
The production of wirewound resistors involves a winding process where a metal wire is carefully wound around a core. The resistance value is adjusted by changing the length and thickness of the wire. After winding, the resistor is often coated with an insulating material to protect it from environmental factors.
2. Thin Film Resistor Production
Thin film resistors are produced using deposition techniques such as sputtering or evaporation. A thin layer of resistive material is deposited onto the substrate, followed by patterning and etching to create the desired resistance value. This process allows for high precision and control over the resistor's characteristics.
3. Thick Film Resistor Production
Thick film resistors are made using a screen printing process, where a paste of conductive material is printed onto a substrate. The printed resistors are then fired in a kiln to cure the paste, creating a solid layer. This method is cost-effective and allows for mass production.
D. Assembly and Packaging
After fabrication, resistors are assembled and packaged. This involves mounting the resistors onto substrates, which may include circuit boards. Encapsulation and protective coatings are applied to enhance durability and protect against environmental factors.
E. Testing and Calibration
Testing and calibration are critical steps in the production process. Electrical testing methods are employed to verify the resistance values and ensure they meet specifications. Calibration against established standards is conducted to guarantee accuracy. Environmental testing is also performed to assess the resistors' performance under various conditions.
V. Quality Control and Standards Compliance
A. Importance of Quality Control in Resistor Production
Quality control is paramount in resistor production, as it ensures that the final products meet the required specifications and standards. Rigorous testing and inspection processes are implemented at various stages of production to identify and rectify any issues.
B. Industry Standards
Compliance with industry standards, such as ISO and IEC, is essential for resistor manufacturers. These standards provide guidelines for quality management, safety, and performance, ensuring that resistors are reliable and suitable for their intended applications.
C. Testing for Reliability and Longevity
Reliability testing is conducted to assess the long-term performance of resistors. This includes stress testing under extreme conditions to evaluate their durability and longevity. Manufacturers aim to produce resistors that can withstand the rigors of their operating environments.
VI. Innovations and Future Trends in Resistor Production
A. Advances in Materials Science
The field of materials science is continually evolving, leading to the development of new materials with enhanced properties. Innovations in conductive and insulating materials are expected to improve the performance and reliability of resistors.
B. Automation and Smart Manufacturing
Automation is becoming increasingly prevalent in resistor production, streamlining processes and reducing human error. Smart manufacturing technologies, such as IoT and AI, are being integrated into production lines to enhance efficiency and quality control.
C. Environmental Considerations and Sustainability
As the electronics industry faces growing environmental concerns, manufacturers are exploring sustainable practices in resistor production. This includes using eco-friendly materials, reducing waste, and implementing energy-efficient processes.
VII. Conclusion
In summary, the production of resistor standards involves a complex interplay of design, material selection, fabrication techniques, and quality control measures. Understanding these processes is crucial for appreciating the role of resistors in modern electronics. As technology continues to advance, the future of resistor production looks promising, with innovations in materials science, automation, and sustainability paving the way for more efficient and reliable components. Resistor standards will remain a cornerstone of electronic design, ensuring that devices operate accurately and effectively in an ever-evolving technological landscape.
VIII. References
- Academic Journals
- Industry Reports
- Standards Organizations Publications
This blog post provides a comprehensive overview of the common production processes for resistor standards, highlighting the importance of these components in the electronics industry and the intricate processes involved in their production.