What are the Product Standards for Inductors?
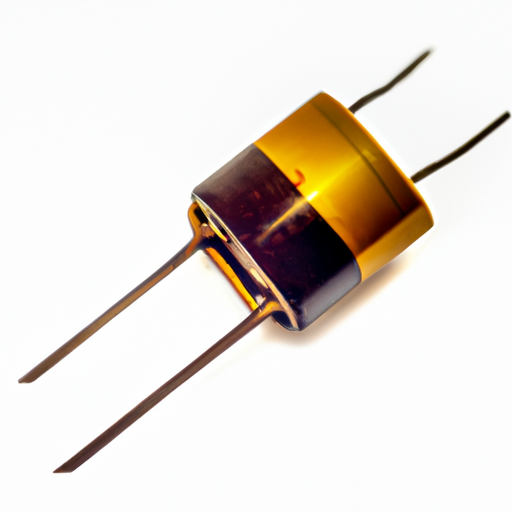
I. Introduction
Inductors are passive electronic components that store energy in a magnetic field when electrical current flows through them. They play a crucial role in various electronic circuits, including power supplies, filters, and oscillators. As the demand for reliable and efficient electronic devices continues to grow, the importance of adhering to product standards for inductors becomes increasingly significant. These standards ensure that inductors meet specific performance criteria, safety requirements, and quality benchmarks, ultimately contributing to the reliability and longevity of electronic systems.
II. Types of Inductors
Inductors come in various types, each designed for specific applications and performance characteristics. Understanding these types is essential for selecting the right inductor for a given application.
A. Air-core Inductors
Air-core inductors are constructed without a magnetic core, relying solely on the air surrounding the coil to provide inductance. They are typically used in high-frequency applications due to their low losses and high self-resonant frequency.
B. Iron-core Inductors
Iron-core inductors utilize a ferromagnetic core to enhance inductance. The core material increases the magnetic field strength, allowing for higher inductance values in a smaller physical size. These inductors are commonly used in power applications.
C. Ferrite-core Inductors
Ferrite-core inductors use ferrite materials, which are ceramic compounds that exhibit magnetic properties. They are particularly effective at high frequencies and are often used in RF applications and power supplies.
D. Toroidal Inductors
Toroidal inductors are wound in a circular shape around a toroidal core. This design minimizes electromagnetic interference and enhances efficiency, making them suitable for various applications, including power supplies and audio equipment.
E. Specialty Inductors
Specialty inductors, such as variable inductors and coupled inductors, are designed for specific functions. Variable inductors allow for adjustable inductance, while coupled inductors are used in applications requiring mutual inductance between two coils.
III. Key Product Standards for Inductors
To ensure the quality and reliability of inductors, several organizations have established product standards. These standards provide guidelines for manufacturers and help consumers make informed choices.
A. International Electrotechnical Commission (IEC) Standards
The IEC is a global organization that develops and publishes international standards for electrical and electronic technologies. Relevant IEC standards for inductors include IEC 60076, which covers power transformers, and IEC 61800, which pertains to adjustable speed electrical power drive systems.
B. Institute of Electrical and Electronics Engineers (IEEE) Standards
The IEEE is a leading organization in the development of standards for electrical and electronic systems. Standards such as IEEE 112, which addresses the testing of inductors, are crucial for ensuring performance and reliability.
C. American National Standards Institute (ANSI) Standards
ANSI oversees the development of voluntary consensus standards for various industries in the United States. ANSI standards relevant to inductors include ANSI C63.4, which covers the measurement of radio-frequency emissions from inductors and other components.
D. Underwriters Laboratories (UL) Standards
UL is a safety certification organization that establishes standards for product safety. UL standards for inductors focus on electrical safety, ensuring that inductors can operate safely under specified conditions.
IV. Key Parameters and Specifications
When evaluating inductors, several key parameters and specifications must be considered to ensure they meet the requirements of a specific application.
A. Inductance Value
The inductance value, measured in henries (H), indicates the inductor's ability to store energy in a magnetic field. It is a critical parameter that influences the performance of the inductor in a circuit.
B. Current Rating
The current rating specifies the maximum continuous current the inductor can handle without overheating or failing. Exceeding this rating can lead to reduced performance or damage.
C. DC Resistance (DCR)
DC resistance is the resistance of the inductor when a direct current flows through it. Lower DCR values are desirable as they minimize power losses and improve efficiency.
D. Saturation Current
Saturation current is the maximum current the inductor can handle before the core material becomes saturated, leading to a significant drop in inductance. This parameter is crucial for applications where high currents are expected.
E. Self-Resonant Frequency (SRF)
The self-resonant frequency is the frequency at which the inductor's inductive reactance equals its capacitive reactance, resulting in resonance. Beyond this frequency, the inductor behaves more like a capacitor, which can affect circuit performance.
F. Quality Factor (Q)
The quality factor (Q) measures the efficiency of the inductor, defined as the ratio of its inductive reactance to its resistance at a specific frequency. A higher Q indicates lower losses and better performance.
G. Temperature Coefficient
The temperature coefficient indicates how the inductance value changes with temperature. This parameter is essential for applications where temperature variations are expected.
H. Insulation Resistance
Insulation resistance measures the resistance between the inductor's windings and its core or casing. High insulation resistance is crucial for preventing short circuits and ensuring safety.
V. Testing and Compliance
To ensure that inductors meet the required standards, various testing methods are employed.
A. Testing Methods for Inductors
1. **Inductance Measurement**: This involves measuring the inductance value using specialized equipment to ensure it meets specified tolerances.
2. **Current Rating Tests**: These tests determine the maximum current the inductor can handle without overheating or failing.
3. **Thermal Testing**: Thermal tests assess the inductor's performance under varying temperature conditions, ensuring it operates safely within its specified limits.
B. Compliance with Standards
Compliance with established standards is vital for manufacturers and consumers alike. It ensures that inductors meet safety and performance criteria, reducing the risk of failure in electronic systems. Certification processes often involve third-party testing and verification to confirm compliance.
VI. Applications of Inductors
Inductors are used in a wide range of applications across various industries, including:
A. Power Supplies
Inductors are essential components in power supply circuits, where they help regulate voltage and current, filter noise, and store energy.
B. RF Applications
In radio frequency (RF) applications, inductors are used in tuning circuits, oscillators, and filters to control signal frequencies and improve performance.
C. Filters and Oscillators
Inductors are integral to filter circuits, where they work alongside capacitors to remove unwanted frequencies. They are also used in oscillators to generate specific frequencies.
D. Energy Storage Systems
Inductors play a crucial role in energy storage systems, such as inductive charging and energy harvesting applications, where they store and release energy as needed.
E. Automotive Applications
In the automotive industry, inductors are used in various systems, including power management, ignition systems, and noise suppression.
VII. Challenges in Standardization
Despite the importance of product standards, several challenges exist in the standardization of inductors.
A. Variability in Applications
The wide range of applications for inductors means that a one-size-fits-all approach to standards may not be feasible. Different applications may require unique specifications and performance criteria.
B. Technological Advancements
Rapid advancements in technology can outpace existing standards, necessitating continuous updates and revisions to ensure they remain relevant and effective.
C. Global Market Considerations
As the electronics market becomes increasingly globalized, harmonizing standards across different regions and countries presents challenges. Variations in regulations and compliance requirements can complicate the manufacturing and certification processes.
VIII. Future Trends in Inductor Standards
Looking ahead, several trends are likely to shape the future of inductor standards.
A. Emerging Technologies
The rise of new technologies, such as electric vehicles, renewable energy systems, and advanced telecommunications, will drive the need for updated standards that address the unique requirements of these applications.
B. Sustainability and Environmental Considerations
As the electronics industry moves towards more sustainable practices, standards will need to incorporate environmental considerations, such as the use of eco-friendly materials and energy-efficient designs.
C. Innovations in Materials and Design
Advancements in materials science and design techniques will lead to the development of more efficient and compact inductors, necessitating updates to existing standards to accommodate these innovations.
IX. Conclusion
In conclusion, product standards for inductors play a vital role in ensuring the quality, reliability, and safety of these essential components in electronic circuits. By adhering to established standards, manufacturers can produce inductors that meet the diverse needs of various applications, while consumers can have confidence in the performance of the products they use. As technology continues to evolve, the importance of maintaining and updating these standards will only grow, ensuring that inductors remain a cornerstone of modern electronics. The future of inductor standards will likely be shaped by emerging technologies, sustainability efforts, and innovations in materials and design, paving the way for more efficient and reliable electronic systems.
What are the Product Standards for Inductors?
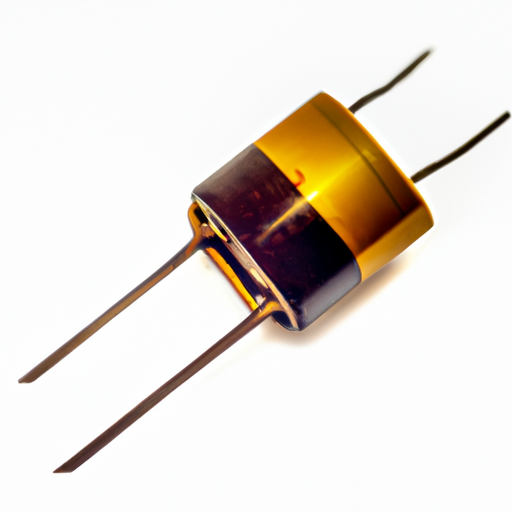
I. Introduction
Inductors are passive electronic components that store energy in a magnetic field when electrical current flows through them. They play a crucial role in various electronic circuits, including power supplies, filters, and oscillators. As the demand for reliable and efficient electronic devices continues to grow, the importance of adhering to product standards for inductors becomes increasingly significant. These standards ensure that inductors meet specific performance criteria, safety requirements, and quality benchmarks, ultimately contributing to the reliability and longevity of electronic systems.
II. Types of Inductors
Inductors come in various types, each designed for specific applications and performance characteristics. Understanding these types is essential for selecting the right inductor for a given application.
A. Air-core Inductors
Air-core inductors are constructed without a magnetic core, relying solely on the air surrounding the coil to provide inductance. They are typically used in high-frequency applications due to their low losses and high self-resonant frequency.
B. Iron-core Inductors
Iron-core inductors utilize a ferromagnetic core to enhance inductance. The core material increases the magnetic field strength, allowing for higher inductance values in a smaller physical size. These inductors are commonly used in power applications.
C. Ferrite-core Inductors
Ferrite-core inductors use ferrite materials, which are ceramic compounds that exhibit magnetic properties. They are particularly effective at high frequencies and are often used in RF applications and power supplies.
D. Toroidal Inductors
Toroidal inductors are wound in a circular shape around a toroidal core. This design minimizes electromagnetic interference and enhances efficiency, making them suitable for various applications, including power supplies and audio equipment.
E. Specialty Inductors
Specialty inductors, such as variable inductors and coupled inductors, are designed for specific functions. Variable inductors allow for adjustable inductance, while coupled inductors are used in applications requiring mutual inductance between two coils.
III. Key Product Standards for Inductors
To ensure the quality and reliability of inductors, several organizations have established product standards. These standards provide guidelines for manufacturers and help consumers make informed choices.
A. International Electrotechnical Commission (IEC) Standards
The IEC is a global organization that develops and publishes international standards for electrical and electronic technologies. Relevant IEC standards for inductors include IEC 60076, which covers power transformers, and IEC 61800, which pertains to adjustable speed electrical power drive systems.
B. Institute of Electrical and Electronics Engineers (IEEE) Standards
The IEEE is a leading organization in the development of standards for electrical and electronic systems. Standards such as IEEE 112, which addresses the testing of inductors, are crucial for ensuring performance and reliability.
C. American National Standards Institute (ANSI) Standards
ANSI oversees the development of voluntary consensus standards for various industries in the United States. ANSI standards relevant to inductors include ANSI C63.4, which covers the measurement of radio-frequency emissions from inductors and other components.
D. Underwriters Laboratories (UL) Standards
UL is a safety certification organization that establishes standards for product safety. UL standards for inductors focus on electrical safety, ensuring that inductors can operate safely under specified conditions.
IV. Key Parameters and Specifications
When evaluating inductors, several key parameters and specifications must be considered to ensure they meet the requirements of a specific application.
A. Inductance Value
The inductance value, measured in henries (H), indicates the inductor's ability to store energy in a magnetic field. It is a critical parameter that influences the performance of the inductor in a circuit.
B. Current Rating
The current rating specifies the maximum continuous current the inductor can handle without overheating or failing. Exceeding this rating can lead to reduced performance or damage.
C. DC Resistance (DCR)
DC resistance is the resistance of the inductor when a direct current flows through it. Lower DCR values are desirable as they minimize power losses and improve efficiency.
D. Saturation Current
Saturation current is the maximum current the inductor can handle before the core material becomes saturated, leading to a significant drop in inductance. This parameter is crucial for applications where high currents are expected.
E. Self-Resonant Frequency (SRF)
The self-resonant frequency is the frequency at which the inductor's inductive reactance equals its capacitive reactance, resulting in resonance. Beyond this frequency, the inductor behaves more like a capacitor, which can affect circuit performance.
F. Quality Factor (Q)
The quality factor (Q) measures the efficiency of the inductor, defined as the ratio of its inductive reactance to its resistance at a specific frequency. A higher Q indicates lower losses and better performance.
G. Temperature Coefficient
The temperature coefficient indicates how the inductance value changes with temperature. This parameter is essential for applications where temperature variations are expected.
H. Insulation Resistance
Insulation resistance measures the resistance between the inductor's windings and its core or casing. High insulation resistance is crucial for preventing short circuits and ensuring safety.
V. Testing and Compliance
To ensure that inductors meet the required standards, various testing methods are employed.
A. Testing Methods for Inductors
1. **Inductance Measurement**: This involves measuring the inductance value using specialized equipment to ensure it meets specified tolerances.
2. **Current Rating Tests**: These tests determine the maximum current the inductor can handle without overheating or failing.
3. **Thermal Testing**: Thermal tests assess the inductor's performance under varying temperature conditions, ensuring it operates safely within its specified limits.
B. Compliance with Standards
Compliance with established standards is vital for manufacturers and consumers alike. It ensures that inductors meet safety and performance criteria, reducing the risk of failure in electronic systems. Certification processes often involve third-party testing and verification to confirm compliance.
VI. Applications of Inductors
Inductors are used in a wide range of applications across various industries, including:
A. Power Supplies
Inductors are essential components in power supply circuits, where they help regulate voltage and current, filter noise, and store energy.
B. RF Applications
In radio frequency (RF) applications, inductors are used in tuning circuits, oscillators, and filters to control signal frequencies and improve performance.
C. Filters and Oscillators
Inductors are integral to filter circuits, where they work alongside capacitors to remove unwanted frequencies. They are also used in oscillators to generate specific frequencies.
D. Energy Storage Systems
Inductors play a crucial role in energy storage systems, such as inductive charging and energy harvesting applications, where they store and release energy as needed.
E. Automotive Applications
In the automotive industry, inductors are used in various systems, including power management, ignition systems, and noise suppression.
VII. Challenges in Standardization
Despite the importance of product standards, several challenges exist in the standardization of inductors.
A. Variability in Applications
The wide range of applications for inductors means that a one-size-fits-all approach to standards may not be feasible. Different applications may require unique specifications and performance criteria.
B. Technological Advancements
Rapid advancements in technology can outpace existing standards, necessitating continuous updates and revisions to ensure they remain relevant and effective.
C. Global Market Considerations
As the electronics market becomes increasingly globalized, harmonizing standards across different regions and countries presents challenges. Variations in regulations and compliance requirements can complicate the manufacturing and certification processes.
VIII. Future Trends in Inductor Standards
Looking ahead, several trends are likely to shape the future of inductor standards.
A. Emerging Technologies
The rise of new technologies, such as electric vehicles, renewable energy systems, and advanced telecommunications, will drive the need for updated standards that address the unique requirements of these applications.
B. Sustainability and Environmental Considerations
As the electronics industry moves towards more sustainable practices, standards will need to incorporate environmental considerations, such as the use of eco-friendly materials and energy-efficient designs.
C. Innovations in Materials and Design
Advancements in materials science and design techniques will lead to the development of more efficient and compact inductors, necessitating updates to existing standards to accommodate these innovations.
IX. Conclusion
In conclusion, product standards for inductors play a vital role in ensuring the quality, reliability, and safety of these essential components in electronic circuits. By adhering to established standards, manufacturers can produce inductors that meet the diverse needs of various applications, while consumers can have confidence in the performance of the products they use. As technology continues to evolve, the importance of maintaining and updating these standards will only grow, ensuring that inductors remain a cornerstone of modern electronics. The future of inductor standards will likely be shaped by emerging technologies, sustainability efforts, and innovations in materials and design, paving the way for more efficient and reliable electronic systems.