The Production Process of Mainstream Film Capacitors
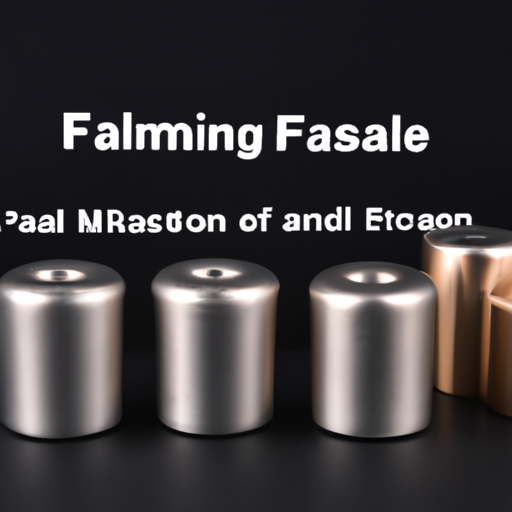
I. Introduction
A. Definition of Film Capacitors
Film capacitors are passive electronic components that store electrical energy in an electric field. They are constructed using thin plastic films as the dielectric material, which separates two conductive plates. This design allows film capacitors to exhibit excellent electrical characteristics, making them suitable for various applications in electronic circuits.
B. Importance of Film Capacitors in Electronics
Film capacitors are widely used in electronic devices due to their reliability, stability, and low loss characteristics. They are essential in applications such as power supplies, audio equipment, and signal processing circuits. Their ability to handle high voltages and temperatures, along with their long lifespan, makes them a preferred choice for engineers and designers in the electronics industry.
C. Overview of the Production Process
The production of film capacitors involves several critical steps, from sourcing raw materials to final assembly and packaging. Understanding this process is essential for appreciating the quality and performance of the capacitors used in modern electronics.
II. Types of Film Capacitors
A. Polyester Film Capacitors
Polyester film capacitors are among the most common types, known for their cost-effectiveness and versatility. They are often used in applications where moderate capacitance and voltage ratings are required.
B. Polypropylene Film Capacitors
Polypropylene film capacitors offer superior performance in terms of low loss and high-frequency applications. They are commonly used in audio and RF circuits due to their excellent stability and low dielectric absorption.
C. Polycarbonate Film Capacitors
Although less common today due to the availability of more efficient materials, polycarbonate film capacitors are valued for their high reliability and stability over a wide temperature range.
D. Other Variants
Other types of film capacitors include polystyrene and fluoropolymer capacitors, each with unique properties that make them suitable for specific applications.
III. Raw Materials
A. Dielectric Films
1. Types of Dielectric Materials
The dielectric material is crucial in determining the performance of film capacitors. Common materials include polyester, polypropylene, and polycarbonate, each offering different electrical and thermal properties.
2. Properties of Dielectric Films
Dielectric films must possess high insulation resistance, low dielectric loss, and stability under varying temperature and voltage conditions. These properties ensure that the capacitor functions effectively over its intended lifespan.
B. Metal Foils
1. Types of Metals Used
Aluminum and copper are the most commonly used metals for the conductive plates in film capacitors. Aluminum is favored for its lightweight and cost-effectiveness, while copper is chosen for its superior conductivity.
2. Importance of Metal Foils in Capacitor Functionality
The metal foils play a critical role in the capacitor's ability to store and release electrical energy. The quality and thickness of these foils directly impact the capacitor's capacitance and voltage ratings.
C. Additional Materials
1. Adhesives
Adhesives are used to bond the dielectric films and metal foils together, ensuring structural integrity during the winding and encapsulation processes.
2. Protective Coatings
Protective coatings are applied to enhance the durability of the capacitors, providing resistance against environmental factors such as moisture and dust.
IV. Production Process
A. Film Preparation
1. Manufacturing of Dielectric Films
The production of dielectric films begins with the extrusion or casting of the chosen polymer material. This process involves heating the polymer until it becomes pliable, then forming it into thin sheets.
2. Thickness and Quality Control
Once the films are produced, they undergo rigorous quality control to ensure they meet specified thickness and electrical properties. This step is crucial, as variations can affect the capacitor's performance.
B. Foil Preparation
1. Sourcing and Processing Metal Foils
Metal foils are sourced from suppliers and processed to achieve the desired thickness and purity. This may involve rolling, annealing, and cutting the foils to size.
2. Surface Treatment for Enhanced Conductivity
To improve conductivity, the metal foils may undergo surface treatments such as etching or plating. These processes enhance the surface area and ensure better electrical contact with the dielectric material.
C. Winding Process
1. Layering of Dielectric and Metal Foils
The winding process involves layering the dielectric films and metal foils in a precise manner. This configuration determines the capacitor's capacitance and voltage rating.
2. Techniques for Winding Capacitors
Various winding techniques, such as spiral or cylindrical winding, are employed depending on the design requirements. Automated winding machines are often used to ensure consistency and precision.
D. Encapsulation
1. Methods of Encapsulation
After winding, the capacitors are encapsulated using methods such as resin potting or heat-shrink tubing. This step protects the internal components from environmental damage.
2. Importance of Encapsulation for Durability
Encapsulation is vital for ensuring the longevity and reliability of film capacitors. It prevents moisture ingress and physical damage, which can lead to capacitor failure.
E. Electrical Testing
1. Testing for Capacitance and Voltage Ratings
Once encapsulated, the capacitors undergo electrical testing to verify their capacitance, voltage ratings, and leakage current. This testing ensures that each capacitor meets the required specifications.
2. Quality Assurance Procedures
Quality assurance procedures are implemented throughout the production process to identify and rectify any defects. This includes regular inspections and testing at various stages of production.
V. Final Assembly and Packaging
A. Final Inspection
1. Visual and Functional Checks
Before packaging, each capacitor undergoes a final inspection, which includes visual checks for physical defects and functional tests to ensure proper operation.
2. Compliance with Industry Standards
Capacitors must comply with industry standards such as IEC and UL to ensure safety and performance. Compliance is verified through documentation and testing.
B. Packaging Techniques
1. Protective Packaging for Transport
Capacitors are packaged using protective materials to prevent damage during transport. This may include anti-static bags, foam inserts, and sturdy boxes.
2. Labeling and Documentation
Each package is labeled with essential information, including part numbers, specifications, and handling instructions. Documentation is provided to ensure traceability and compliance.
VI. Environmental Considerations
A. Sustainable Practices in Production
Manufacturers are increasingly adopting sustainable practices in the production of film capacitors. This includes using eco-friendly materials and reducing waste through efficient manufacturing processes.
B. Recycling and Disposal of Film Capacitors
At the end of their life cycle, film capacitors can be recycled to recover valuable materials. Manufacturers are encouraged to implement take-back programs to facilitate proper disposal and recycling.
C. Regulatory Compliance
Compliance with environmental regulations is essential for manufacturers. This includes adhering to directives such as RoHS (Restriction of Hazardous Substances) to minimize the environmental impact of electronic waste.
VII. Conclusion
A. Summary of the Production Process
The production process of mainstream film capacitors involves several critical steps, from sourcing raw materials to final assembly and packaging. Each stage is essential for ensuring the quality and performance of the capacitors.
B. Future Trends in Film Capacitor Manufacturing
As technology advances, the demand for higher performance and more efficient film capacitors continues to grow. Future trends may include the development of new dielectric materials and manufacturing techniques that enhance performance while reducing environmental impact.
C. The Role of Film Capacitors in Advancing Technology
Film capacitors play a vital role in the advancement of technology, enabling the development of more efficient and reliable electronic devices. Their continued evolution will be essential in meeting the demands of future applications.
VIII. References
A. Academic Journals
- Journal of Electronic Materials
- IEEE Transactions on Electron Devices
B. Industry Reports
- Market Research Reports on Capacitor Technologies
- Industry Analysis from Electronics Manufacturers
C. Manufacturer Guidelines
- Technical Specifications from Leading Capacitor Manufacturers
- Best Practices for Capacitor Design and Application
---
This blog post provides a comprehensive overview of the production process of mainstream film capacitors, highlighting the importance of each step in ensuring the quality and reliability of these essential electronic components.
The Production Process of Mainstream Film Capacitors
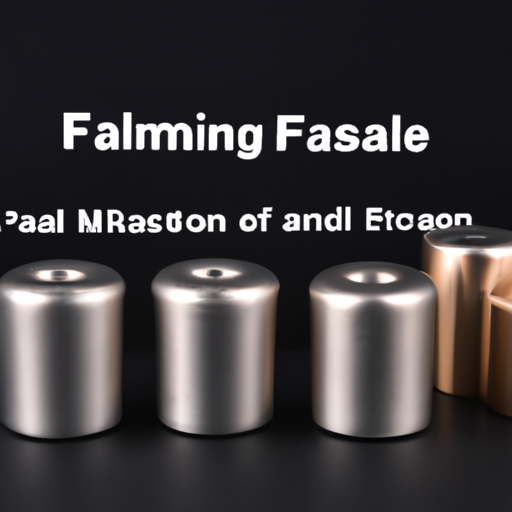
I. Introduction
A. Definition of Film Capacitors
Film capacitors are passive electronic components that store electrical energy in an electric field. They are constructed using thin plastic films as the dielectric material, which separates two conductive plates. This design allows film capacitors to exhibit excellent electrical characteristics, making them suitable for various applications in electronic circuits.
B. Importance of Film Capacitors in Electronics
Film capacitors are widely used in electronic devices due to their reliability, stability, and low loss characteristics. They are essential in applications such as power supplies, audio equipment, and signal processing circuits. Their ability to handle high voltages and temperatures, along with their long lifespan, makes them a preferred choice for engineers and designers in the electronics industry.
C. Overview of the Production Process
The production of film capacitors involves several critical steps, from sourcing raw materials to final assembly and packaging. Understanding this process is essential for appreciating the quality and performance of the capacitors used in modern electronics.
II. Types of Film Capacitors
A. Polyester Film Capacitors
Polyester film capacitors are among the most common types, known for their cost-effectiveness and versatility. They are often used in applications where moderate capacitance and voltage ratings are required.
B. Polypropylene Film Capacitors
Polypropylene film capacitors offer superior performance in terms of low loss and high-frequency applications. They are commonly used in audio and RF circuits due to their excellent stability and low dielectric absorption.
C. Polycarbonate Film Capacitors
Although less common today due to the availability of more efficient materials, polycarbonate film capacitors are valued for their high reliability and stability over a wide temperature range.
D. Other Variants
Other types of film capacitors include polystyrene and fluoropolymer capacitors, each with unique properties that make them suitable for specific applications.
III. Raw Materials
A. Dielectric Films
1. Types of Dielectric Materials
The dielectric material is crucial in determining the performance of film capacitors. Common materials include polyester, polypropylene, and polycarbonate, each offering different electrical and thermal properties.
2. Properties of Dielectric Films
Dielectric films must possess high insulation resistance, low dielectric loss, and stability under varying temperature and voltage conditions. These properties ensure that the capacitor functions effectively over its intended lifespan.
B. Metal Foils
1. Types of Metals Used
Aluminum and copper are the most commonly used metals for the conductive plates in film capacitors. Aluminum is favored for its lightweight and cost-effectiveness, while copper is chosen for its superior conductivity.
2. Importance of Metal Foils in Capacitor Functionality
The metal foils play a critical role in the capacitor's ability to store and release electrical energy. The quality and thickness of these foils directly impact the capacitor's capacitance and voltage ratings.
C. Additional Materials
1. Adhesives
Adhesives are used to bond the dielectric films and metal foils together, ensuring structural integrity during the winding and encapsulation processes.
2. Protective Coatings
Protective coatings are applied to enhance the durability of the capacitors, providing resistance against environmental factors such as moisture and dust.
IV. Production Process
A. Film Preparation
1. Manufacturing of Dielectric Films
The production of dielectric films begins with the extrusion or casting of the chosen polymer material. This process involves heating the polymer until it becomes pliable, then forming it into thin sheets.
2. Thickness and Quality Control
Once the films are produced, they undergo rigorous quality control to ensure they meet specified thickness and electrical properties. This step is crucial, as variations can affect the capacitor's performance.
B. Foil Preparation
1. Sourcing and Processing Metal Foils
Metal foils are sourced from suppliers and processed to achieve the desired thickness and purity. This may involve rolling, annealing, and cutting the foils to size.
2. Surface Treatment for Enhanced Conductivity
To improve conductivity, the metal foils may undergo surface treatments such as etching or plating. These processes enhance the surface area and ensure better electrical contact with the dielectric material.
C. Winding Process
1. Layering of Dielectric and Metal Foils
The winding process involves layering the dielectric films and metal foils in a precise manner. This configuration determines the capacitor's capacitance and voltage rating.
2. Techniques for Winding Capacitors
Various winding techniques, such as spiral or cylindrical winding, are employed depending on the design requirements. Automated winding machines are often used to ensure consistency and precision.
D. Encapsulation
1. Methods of Encapsulation
After winding, the capacitors are encapsulated using methods such as resin potting or heat-shrink tubing. This step protects the internal components from environmental damage.
2. Importance of Encapsulation for Durability
Encapsulation is vital for ensuring the longevity and reliability of film capacitors. It prevents moisture ingress and physical damage, which can lead to capacitor failure.
E. Electrical Testing
1. Testing for Capacitance and Voltage Ratings
Once encapsulated, the capacitors undergo electrical testing to verify their capacitance, voltage ratings, and leakage current. This testing ensures that each capacitor meets the required specifications.
2. Quality Assurance Procedures
Quality assurance procedures are implemented throughout the production process to identify and rectify any defects. This includes regular inspections and testing at various stages of production.
V. Final Assembly and Packaging
A. Final Inspection
1. Visual and Functional Checks
Before packaging, each capacitor undergoes a final inspection, which includes visual checks for physical defects and functional tests to ensure proper operation.
2. Compliance with Industry Standards
Capacitors must comply with industry standards such as IEC and UL to ensure safety and performance. Compliance is verified through documentation and testing.
B. Packaging Techniques
1. Protective Packaging for Transport
Capacitors are packaged using protective materials to prevent damage during transport. This may include anti-static bags, foam inserts, and sturdy boxes.
2. Labeling and Documentation
Each package is labeled with essential information, including part numbers, specifications, and handling instructions. Documentation is provided to ensure traceability and compliance.
VI. Environmental Considerations
A. Sustainable Practices in Production
Manufacturers are increasingly adopting sustainable practices in the production of film capacitors. This includes using eco-friendly materials and reducing waste through efficient manufacturing processes.
B. Recycling and Disposal of Film Capacitors
At the end of their life cycle, film capacitors can be recycled to recover valuable materials. Manufacturers are encouraged to implement take-back programs to facilitate proper disposal and recycling.
C. Regulatory Compliance
Compliance with environmental regulations is essential for manufacturers. This includes adhering to directives such as RoHS (Restriction of Hazardous Substances) to minimize the environmental impact of electronic waste.
VII. Conclusion
A. Summary of the Production Process
The production process of mainstream film capacitors involves several critical steps, from sourcing raw materials to final assembly and packaging. Each stage is essential for ensuring the quality and performance of the capacitors.
B. Future Trends in Film Capacitor Manufacturing
As technology advances, the demand for higher performance and more efficient film capacitors continues to grow. Future trends may include the development of new dielectric materials and manufacturing techniques that enhance performance while reducing environmental impact.
C. The Role of Film Capacitors in Advancing Technology
Film capacitors play a vital role in the advancement of technology, enabling the development of more efficient and reliable electronic devices. Their continued evolution will be essential in meeting the demands of future applications.
VIII. References
A. Academic Journals
- Journal of Electronic Materials
- IEEE Transactions on Electron Devices
B. Industry Reports
- Market Research Reports on Capacitor Technologies
- Industry Analysis from Electronics Manufacturers
C. Manufacturer Guidelines
- Technical Specifications from Leading Capacitor Manufacturers
- Best Practices for Capacitor Design and Application
---
This blog post provides a comprehensive overview of the production process of mainstream film capacitors, highlighting the importance of each step in ensuring the quality and reliability of these essential electronic components.